Balancing Services
Unbalance in rotating components could lead to a catastrophic failure and result in threats to machinery and personal safety.
Despite its apparent simplicity, precisely balancing a rotor requires a subtle yet absolute expertise. Not all balancing service providers are “equal”, and capable of performing the necessary level of quality and consistency in their work. Improper or insufficient balancing can cause even more issues, all of which resulting in higher overall costs. To learn more, read our E-Book "Balancing 101: What you should know about balancing your rotating part" for more information.
-
Balance tooling design
Balance tooling design
A balancing job is only as good as the tooling used to perform it. Well-designed tooling should provide a precisely-machined shaft surface to mount the rotor onto the balancing machine, and a purpose-designed mechanism to accurately interface the shaft with the rotor in an accurate and repeatable manner. This detail is often overlooked by customers who are not familiar with balancing processes.
-
Engineering support
Engineering support
Balancing is not an art—it is a science and an engineered process. Correctly installing the balancing machine, calibrating the measurement, and performing a repeatable and accurate unbalance measurement are crucial steps before any unbalance correction can be performed. The methods and operational steps in unbalance correction must be implemented with a full understanding of the damage sensitivity and operation-critical features of the parts to avoid damage and mishandling.
-
Quality assurance
Quality assurance
All planned balancing processes should be double checked by trained members of the quality assurance department, as should all completed balance corrections. This is particularly important for work that involves safety and operation-critical rotating components, as even the slightest mishandling can lead to serious consequences.
-
Balance budget analysis
Balance budget analysis
The effect of the geometric tolerances of given parts are analyzed and the influence on the imbalance of the rotor is estimated using a mathematical model to simulate the manufacturing process, while also comparing more than 10,000 different combinations of tolerance variations. The output from this analysis provides a probabilistic model of the imbalance in the rotor, which can be used to tune the design, minimize scatter, and avoid surprises in your fabrication processes.
-
Precision Machining
Precision Machining
Some balancing work may require very delicate and precise material removal where manual grinding with hand tools is not appropriate. TDI is equipped with state-of-the-art CNC mills and has an expert machinist ready to serve your needs.
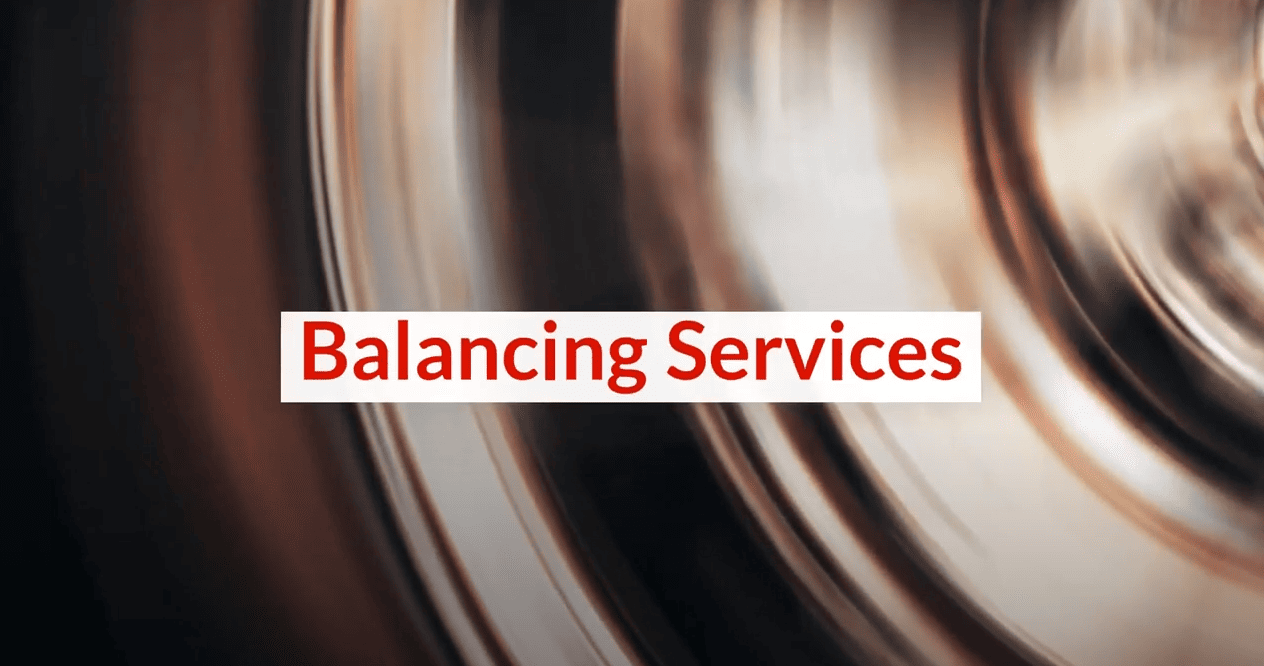
-
One Stop Shop
One Stop Shop
Test Devices is an AS9100 certified service provider. We offer a full range of aerospace quality services associated with the balancing of parts. Test Devices has the in-house capabilities for designing and manufacturing purpose-built precision balance tooling and offering engineering consultations on planning and troubleshooting your balancing needs. We work with a variety of projects sizes ranging from a single part to full production lots.
Contact Us Today -
Quality
Quality
At Test Devices Inc., our experienced quality experts will review the operational plan and workmanship to meet your requirements. All planned balancing processes and completed balance corrections should be double-checked by trained members of the quality assurance department. This is particularly important for work involving safety and operation-critical rotating components, as even the slightest mishandling can lead to serious consequences.
Any balancing work should come with a thorough plan for the prevention of any potential damage to the part during the balancing process. The cost is especially detrimental to delicate and high-value rotating components. Typically, damage is usually caused by one of a few scenarios:
- Mishandling parts during transport
- Errant material removal
- Spark impingement
Over-Speed Spin Testing
Manufacturing processes for some high-speed components require both balancing and over-speed spin testing prior to final installation. Test Devices provides a full range of spin testing services with a quick turnaround.
Balancing Services
Drawings for many precision parts call out very precise depth and width levels, below which material cannot be removed. To ensure compliance to these requirements, for many precision balanced parts, Test Devices includes a final measurement verification step performed by our quality department.